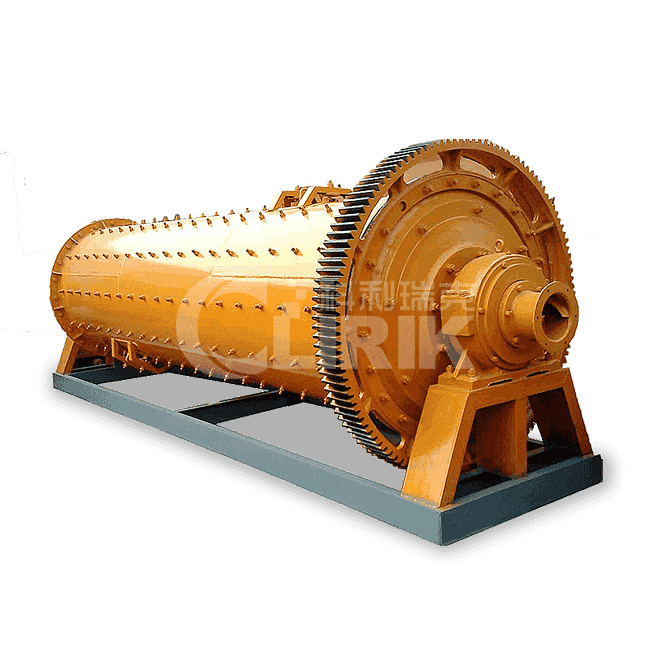
Ball mill is cylindrical grinding equipment, which is widely used in the field of ore milling. The purpose of milling is achieved by the collision of steel balls. It is widely used in the grinding of cement, silicate products, building materials, refractory materials, fertilizers, and various minerals.
Application range: limestone, calcite, calcium carbonate, barite, talc, gypsum, diabase, quartzite, bentonite, etc.
Materials: Calcium carbonate crushing, gypsum powder processing, power plant desulfurization, non-metallic ore pulverizing, pulverized coal preparation, etc.
Capcity: 0.65-17 t/h
Output size: 0.074-0.4 μm
Features of Ball Mill
Ball mill is a piece of cylindrical grinding equipment, which is widely used in the field of ore milling. The purpose of milling is achieved by the collision of steel balls. It is widely used in the grinding of cement, silicate products, building materials, refractory materials, fertilizers, and various minerals.
The ball mill is the key equipment for the material to be crushed and then crushed. It is widely used in cement, silicate products, new building materials, refractory materials, fertilizers, ferrous and non-ferrous metal beneficiation, glass ceramics and other production industries, dry or wet grinding of various ores and other grindable materials.
Ball mills are suitable for grinding various ores and other materials. They are widely used in mineral processing, building materials, and chemical industries. They can be divided into dry and wet grinding methods. two types.
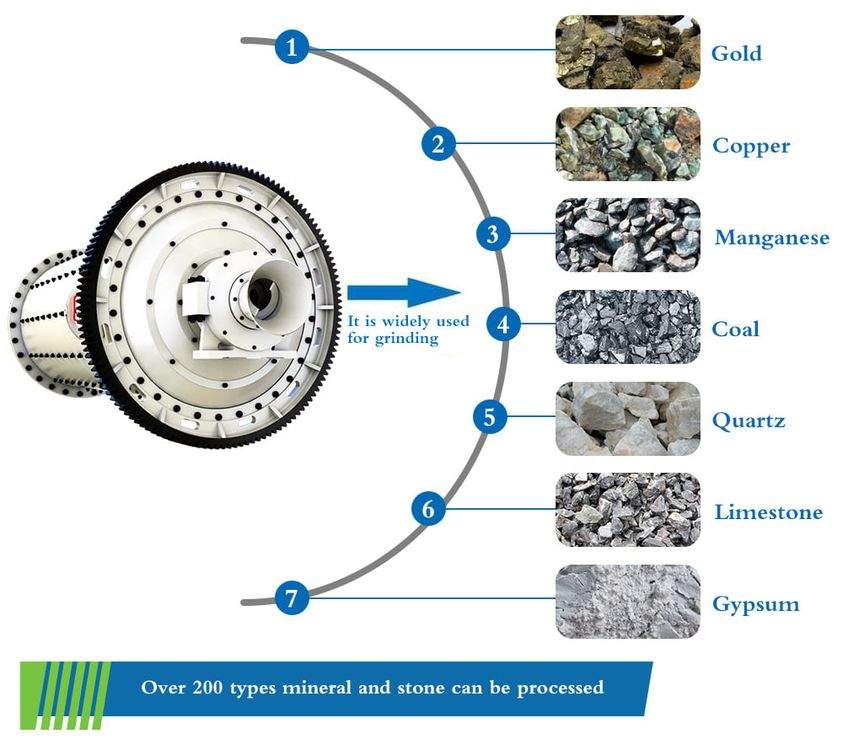
Performance Advantage of Ball Mill
Energy efficient
High safety and reliability
Long service life of wearing parts
Environmentally friendly and clean
Ball Mill Structure and Composition
The ball mill is composed of main parts such as the feeding part, discharging part, rotating part, transmission part (reducer, small transmission gear, motor, electric control).
The hollow shaft is made of cast steel, the inner lining can be removed and replaced, the large rotary gear is processed by casting gear hobbing, and the cylinder is inlaid with a wear-resistant lining plate, which has good wear resistance. The machine runs smoothly and works reliably.
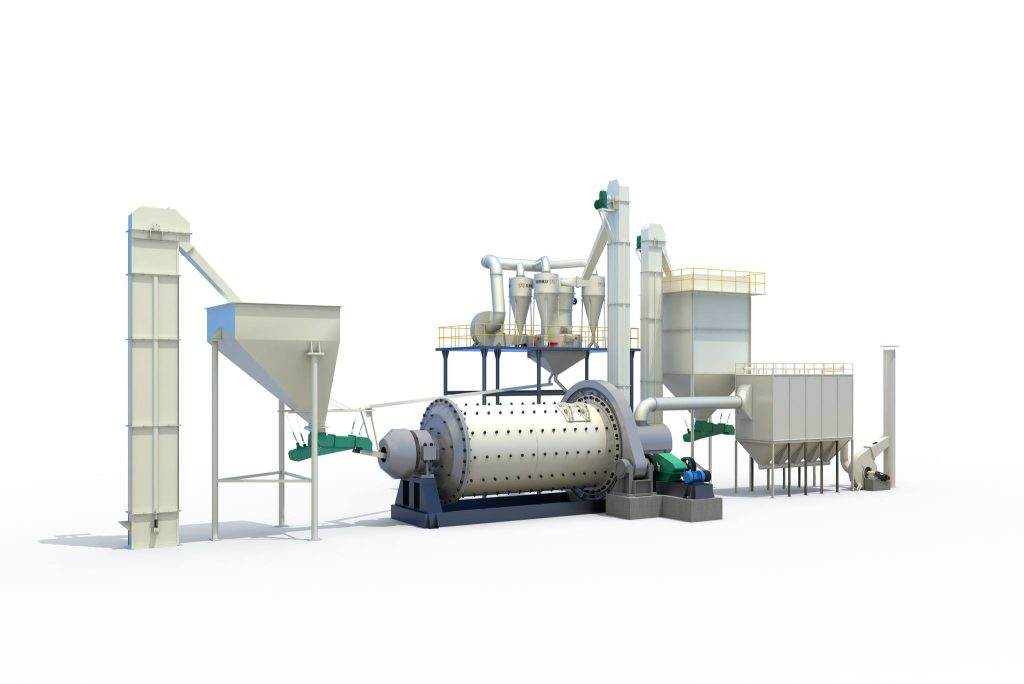
Ball mill host
The main body of the ball mill includes a cylinder, which is inlaid with a lining made of wear-resistant materials, a bearing that carries the cylinder and maintains its rotation, and also has a driving part, such as a motor, and transmission gears, pulleys, V-belts, etc.
Ball mill blades
As for the part called the blade, it is generally not the main part. The inner spiral in the inlet of the component at the feeding end can be called the inner spiral blade, and the inner spiral in the outlet of the component at the discharging end can also be called the inner spiral blade.
In addition, if a screw conveyor is used in the auxiliary equipment at the discharge end, there will be parts called screw blades in the equipment, but strictly speaking, it is no longer a part of the ball mill.
Ball mill selection
According to the material and ore discharge method, dry ball mill and wet grid ball mill can be selected. The energy-saving ball mill adopts self-aligning double-row radial spherical roller bearings, with low running resistance and remarkable energy-saving effect. In the barrel part, a conical barrel is added to the discharge end of the original barrel, which not only increases the effective volume of the mill, but also makes the medium distribution in the barrel more reasonable.
This product is widely used in non-ferrous metal, ferrous metal, non-metal beneficiation field and chemical and building materials industry as material grinding.
Working Principle
Step 1
According to the particle size of the grinding material, the material is loaded into the cylinder by the hollow shaft at the feed end of the ball mill. When the ball mill cylinder rotates, the grinding body is attached to the cylinder liner due to the action of inertia, centrifugal force and frictional force.
It is taken away by the cylinder, and when it is brought to a certain height, it is thrown down due to its own gravity, and the falling grinding body crushes the material in the cylinder like a projectile.
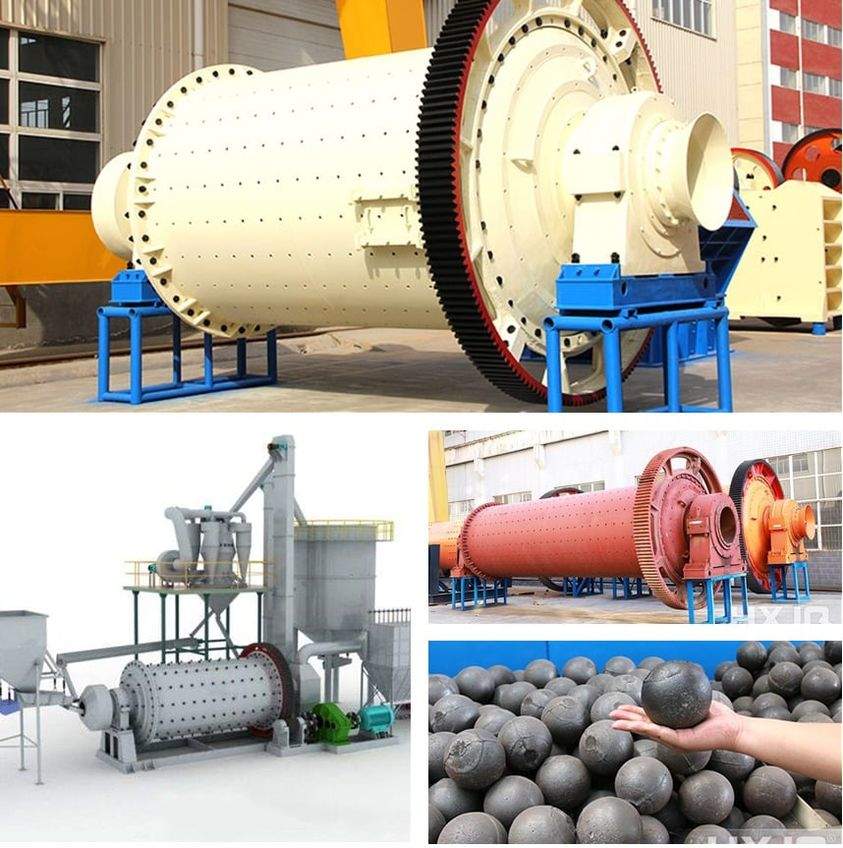
Step 2
The material enters the mill chamber spirally and evenly from the feeding device through the feeding hollow shaft. There are stepped lining plates or corrugated lining plates in the chamber, and various specifications of steel balls are installed inside. The rotation of the cylinder generates centrifugal force to bring the steel balls to a certain height. Falling, pounding and grinding the material. After the material reaches the rough grinding in the warehouse, it enters the second warehouse through the single-layer partition board. The warehouse is inlaid with a flat lining board and has steel balls to further grind the material. The powder is discharged through the discharge grate to complete the grinding operation.
Step 3
During the rotation of the cylinder, the grinding body also has a phenomenon of slipping. During the sliding process, the material is subjected to grinding action. In order to effectively utilize the grinding action, the grinding body cylinder is ground when the particle size of the material is generally 20 mesh. The material is divided into two sections by the partition board, that is, it becomes a double warehouse. When the material enters the warehouse, it is crushed by steel balls. When the material enters the second warehouse, the steel section grinds the material, and the ground and qualified materials are discharged from the hollow shaft at the discharge end. , When grinding materials with small feed particles, such as No. 2 sand slag, coarse fly ash, the barrel of the mill can be a single-silo mill without partitions, and the grinding body can also be made of steel.
Step 4
The raw materials are fed into the hollow cylinder through the hollow journal for grinding, and the cylinder is equipped with grinding media of various diameters (steel balls, steel bars or gravel, etc.). When the cylinder rotates at a certain speed around the horizontal axis, under the action of centrifugal force and frictional force, the medium and raw materials installed in the cylinder will leave the cylinder when the cylinder body reaches a certain height and its own gravity is greater than the centrifugal force. The inner wall is projected to fall or roll down, breaking the ore due to the force of the impact. At the same time, during the rotation of the mill, the sliding movement of the grinding media between each other also produces a grinding effect on the raw materials. The ground material is discharged through the hollow journal.
Technical Parameter
Model | Cylinder Speed (r.p.m) | Loading Capacity (t) | Feeding Size (mm) | Output Size (microns) | Yield (t/h) | Motor Power (KW) | Weight (t) |
---|---|---|---|---|---|---|---|
900×1800 | 38 | 1.5 | ≤20 | 0.075-0.89 | 0.65-2 | 18.5 | 3.6 |
900×3000 | 38 | 2.7 | ≤20 | 0.075-0.89 | 1.1-3.5 | 22 | 4.6 |
1200×2400 | 32 | 3.8 | ≤25 | 0.075-0.6 | 1.5-4.8 | 45 | 12.5 |
1200×3000 | 32 | 5 | ≤25 | 0.074-0.4 | 1.6-5 | 45 | 12.8 |
1200×4500 | 32 | 7 | ≤25 | 0.074-0.4 | 1.6-5.8 | 55 | 13.8 |
1500×3000 | 27 | 8 | ≤25 | 0.074-0.4 | 2-5 | 90 | 17 |
1500×4500 | 27 | 14 | ≤25 | 0.074-0.4 | 3-6 | 110 | 21 |
1500×5700 | 27 | 15 | ≤25 | 0.074-0.4 | 3.5-8 | 132 | 24.7 |
1830×4100 | 24 | 11 | ≤25 | 0.074-0.4 | 4-10 | 180 | 28 |
1830×6400 | 24 | 23 | ≤25 | 0.074-0.4 | 6.5-15 | 210 | 34 |
1830×7000 | 24 | 25 | ≤25 | 0.074-0.4 | 7.5-17 | 245 | 36 |
2100×3600 | 21 | 30 | ≤25 | 0.074-0.4 | 10-22 | 245 | 48.5 |
2200×4500 | 21 | 31 | ≤25 | 0.074-0.4 | 14-26 | 280 | 52.8 |
2200×7000 | 21 | 33 | ≤25 | 0.074-0.4 | 16-29 | 430 | 56 |
Related Products
Coarse, Fine, Ultrafine Powder Grinding Mills
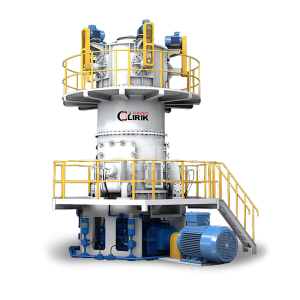
CLUM Ultrafine Powder Vertical Roller Mill
CLUM ultra-fine powder vertical roller mill is mainly suitable for the deep processing of ultra-fine and large-scale powder of non-metallic minerals such as calcite, marble, limestone, talc, barite, brucite, quicklime, gypsum, slag, phosphate, etc.
Capacity: 0.5-45t/h
Finished fineness: 200-3000 mesh
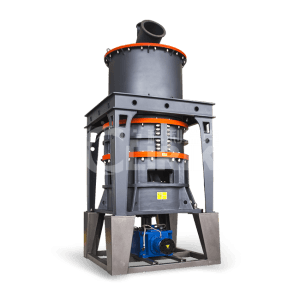
HGM Ultrafine Powder Grinding Mill
HGM Ultrafine Powder Grinding Mill also called ultrafine pulverizer, micro powder grinding mill, limestone grinding mill, calcium carbonate grinding mill. HGM ultrafine powder grinding mill is mainly suitable for superfine powder processing.
Capacity: 0.5-45t/h
Finished fineness: 100-3000 mesh
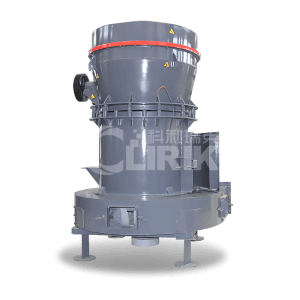
YGM Raymond Roller Grinding Mill
YGM Raymond roller grinding mill is mainly suitable for grinding and processing metallurgy, building materials, chemical industry, mining, and other mineral products.
Capacity: 1.5-40t/h
Finished fineness: 80-600 mesh
How To Operate A Ball Mill?
所需时间: 2 小时
How to operate a ball mill?
- 1. Check before starting the machine.
The inspection work before starting the ball mill is very important. The main inspections are whether there are foreign objects inside the ball mill, whether there are dangerous objects around the ball mill, whether the connecting bolts of the ball mill are loose, whether the transmission device is normal, and whether the lubricating oil is appropriate. need to be dealt with in a timely manner.
- 2. Startup in the specified order
It is very important to operate the ball mill in the prescribed order, followed by the feeder motor, the main engine motor, the high-pressure oil pump, and the low-pressure oil pump, which must be debugged before starting. Within one hour, the ball mill can only be started once, and everything should be carried out in sequence. , which can avoid accidents caused by omissions or irregularities.
- 3. Pay attention to current changes when starting
When starting the ball mill, it is necessary to observe the change of the current. The starting current should not be too large, otherwise, the grid voltage will drop suddenly, which will affect the normal production of other equipment. In severe cases, it will also cause machine failure.
- 4. Pay attention during operation
During the operation of the ball mill, pay attention to observing the current, oil temperature, spindle temperature, voltage, and other data. When feeding, it should be uniform and continuous. Excessive feeding should not be allowed. The amount of water, ore, and steel balls should be added according to the regulations. Check Whether the cylinder is leaking slurry, the temperature of the main shaft should not be greater than 60°С, check the motor and main shaft every half an hour, and deal with any problems in time.
- 5. Clear the mine before shutting down
The stop sequence of the ball mill is first stopped feeding, then stop the main motor, then stop the high-pressure oil pump when the ball mill stops running, then stop the low-pressure oil pump, pay attention to observe the temperature of the bearing, until the ball mill barrel cools to room temperature, the shutdown work is completed.
- 5. Regularly check the use of steel balls
Ball mill steel ball is an important part of ball mill and an important grinding medium. During the grinding process, the steel ball will also be worn to varying degrees. In the long run, if the severely worn steel ball is not replaced in time, it will seriously affect the grinding process. Therefore, after a period of operation, all-steel balls should be selected and replaced with new balls.