Application range: calcium carbonate crushing processing, gypsum powder processing, power plant desulfurization, non-metallic ore pulverizing, coal powder preparation, etc.
Applicable materials: limestone, calcite, calcium carbonate, barite, talc, gypsum, diabase, quartzite, bentonite, etc.
Production capacity 0.5-45t/h
Finished fineness 150-3000 mesh
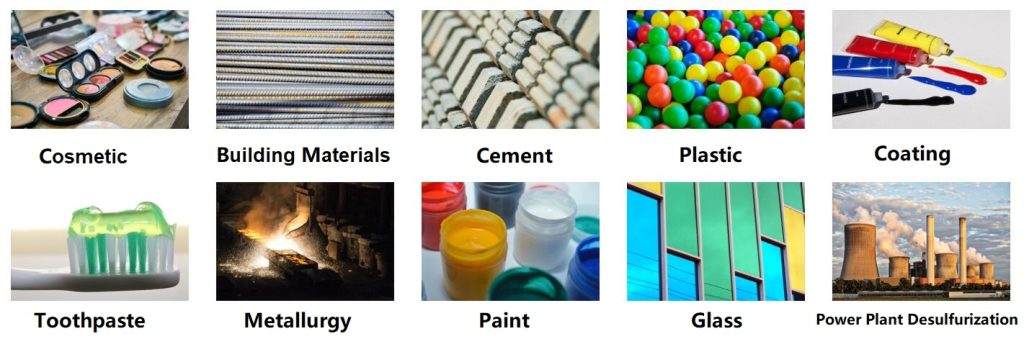
Features of HGM Ultrafine Powder Grinding Mill
HGM Ultrafine Powder Grinding Mill Ultrafine Pulverizer Micro Powder Grinding Mill Limestone Grinding Mill Calcium Carbonate Grinding Mill Marble Grinding Mill Gypsum Grinding Mill Feldspar Grinding Mill
HGM Ultrafine Powder Grinding Mill also called ultrafine pulverizer, micro powder grinding mill, limestone grinding mill, calcium carbonate grinding mill, talc grinding mill, barite grinding mill, gypsum grinding mill, marble grinding mill, feldspar grinding mill, fluorite grinding mill.
Applicable Materials
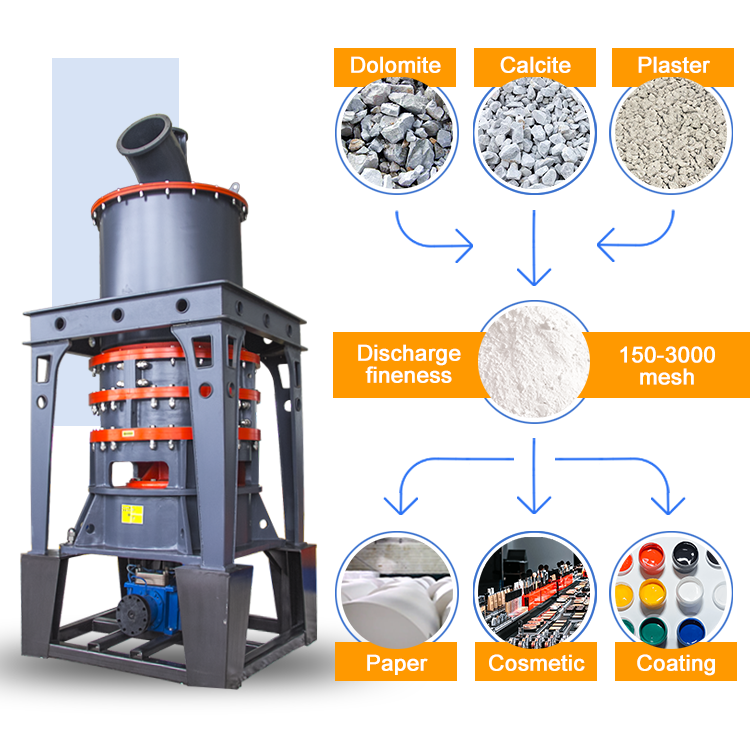
HGM ultrafine powder grinding mill is mainly suitable for superfine powder processing of non-flammable and explosive brittle materials with medium and low hardness, Mohs hardness ≤6, such as calcite, chalk, limestone, carbon black, kaolin, bentonite, Talc, mica, magnesite, illite, pyrophyllite, vermiculite, sepiolite, attapulgite, rectorite, diatomite, barite, gypsum, alumite, graphite, fluorite, phosphate rock, potassium ore, pumice and other more than 100 kinds of materials, the particle size of fine powder products can be adjusted arbitrarily between 325-3000 mesh, and the output can reach 0.4-45 tons per hour.
Performance Advantage of HGM Ultrafine Powder Grinding Mill
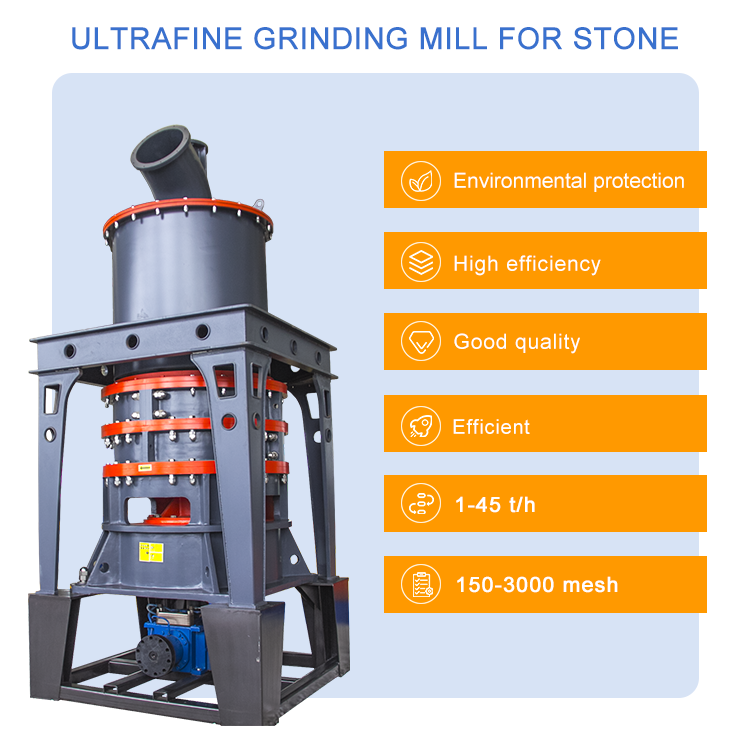
1. Energy efficientIn the case of the same fineness of finished products and the same motor power, the output is more than double that of jet mill, stirring mill and ball mill.
2. Long service life of wearing partsGrinding rollers and grinding rings are forged with special materials, which greatly improves the utilization. Generally, it can last for more than one year. When processing calcium carbonate and calcite, the service life can reach 2-5 years.
3. High safety and reliabilityBecause there is no rolling bearing and no screw in the grinding chamber, there is no problem that the bearing and its seals are easily damaged, and there is no problem that the screw is easy to loosen and damage the machine.
4. Environmentally friendly and cleanThe pulse dust collector is used to capture dust, and the muffler is used to reduce noise, which is environmentally friendly and clean.
Structure and Composition of HGM Ultrafine Powder Grinding Mill
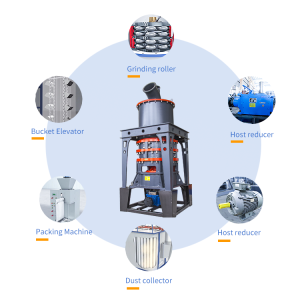
The main part of the HGM ultrafine powder grinding mill is composed of the main engine, the reducer, the analyzer, the fan, the bypass powder collector, the maintenance platform, and the electric control cabinet. The auxiliary machine part consists of jaw crusher, bucket elevator, electromagnetic vibrating feeder, storage bin, and so on.
The grinding mill production line usually includes hammer crusher, bucket elevator, storage bin, vibrating feeder, ultrafine powder grinding mill host, frequency conversion classifier, double cyclone powder collector, pulse dust removal system, high-pressure fan, air compressor, electrical control system, etc. The bulk material is crushed by the hammer crusher into a feed size (about 1cm) suitable for the operation of the ultra-fine pulverizer, and then the fineness suitable for the production requirements is achieved by adjusting the rotation speed of the analyzer of the pulverizer, and it is manually packaged into bags, You can also configure automatic micro powder baler and choose different types of pulverizers according to your needs.
What Should Be Paid Attention to When The Ultrafine Mill Is Working?
1. Always check the bearing temperature. If the temperature is too high, check whether the lubrication and transmission parts are normal and whether the rolling distance is too tight. Find out the cause in time, take corresponding measures, and stop inspection when the situation is serious.
2. Always check the tightness of the transmission belt. If the belt is too loose, it will reduce the transmission efficiency and affect the grinding effect. If the belt is too tight, it will easily cause the bearing to heat up, increase the power consumption, and reduce the service life of the transmission belt.
3. Various transmission parts must be fastened and reliable, special tools should be used for disassembly or installation, and direct hitting with tools such as hand hammers is prohibited.
5. Don’t forget to check the pneumatic components. After the plastic mill is turned on, you should always check the pneumatic components in the air circuit, whether there is air leakage or damage in the air circuit, and the connection. At the same time, check whether the air supply pressure meets the requirements. The use of the machine should also be checked frequently. If it is found to be too tight, too loose, jumping, deviation, serious wear, etc., it should be adjusted, repaired, or replaced in time. The oil storage of the lubricator in the air source triplet should be checked regularly, and 20# spindle oil must be added to prevent the small holes of the pipeline from being blocked.
HGM Ultrafine Powder Grinding Mill Working Principle
When working, the main motor drives the main shaft and the turntable to rotate through the reducer, and the roller pins on the edge of the turntable drive dozens of grinding rollers to roll in the grinding ring raceway.
The bulk material is crushed into small particles by the hammer crusher, and then sent to the storage bin by elevator, and then sent to the bulk material tray on the upper part of the turntable evenly through the vibrating feeder and the inclined feeding pipe.
The material is scattered to the periphery of the circle under the action of centrifugal force and falls into the raceway of the grinding ring. It is impacted, rolled, and ground by the ring roller. It is sucked into the machine, and the pulverized material is brought into the classifier.
The rotating impeller in the powder concentrator makes the coarse material fall back for regrinding, and the fine powder that meets the requirements enters the cyclone powder collector with the airflow and is discharged from the discharge valve at the lower part to be the finished product, while the airflow with a small amount of fine dust passes through. After the pulse dust collector, it is discharged through the fan and the muffler.
Technical Parameter
Model | Average Diameter (mm) |
Number of Rings (pcs) |
Feed Size Feeding Size (mm) |
Output Size Range (mesh) |
Finished Product Capacity (t/h) |
Dimensions (L*W*H) (mm) |
Installed Power (KW) |
---|---|---|---|---|---|---|---|
HGM80 | 800 | 3 | ≤10 | 150-3000 | 0.5-6 | 8605*4139x6050 | 142 |
HGM80A | 800 | 3 | ≤10 | 150-3000 | 0.5-6 | 10454*3393*6626 | 142 |
HGM90L | 900 | 4 | ≤10 | 150-3000 | 0.8-7 | 11735*3952*7525 | 180 |
HGM100L-Ⅱ | 1000 | 4 | ≤15 | 150-3000 | 1.2-10.5 | 14507*3633*7562 | 242 |
HGM100P | 1000 | 4 | ≤15 | 150-3000 | 1.2-11.5 | 14362*4200*7562 | 267 |
HGM125L | 1250 | 4 | ≤20 | 150-2000 | 2.5-20.5 | 19261*4406*8591 | 401 |
HGM1680L | 1680 | 4 | ≤20 | 150-1500 | 5-45 | 25067*5414*9007 | 665-685 |
The specific equipment parameters are subject to the actual equipment | Mainframe and Dust Collector System Only | Other Options |
Note: This capacity range is based on domestic calcium carbonate materials, and the differences between different materials will vary.
Factory Tour-HGM Ultrafine Powder Grinding Mill
Welcome to visit the factory online with our cameras.
If you are interested in our HGM ultrafine powder grinding mill. Please contact us freely.
Email: sales@clirik.com
WhatsApp: +8613512155195